eRDM - Dynamic Railway Diagnostic System
Solutions
Candid has created state-of-the-art and cost-effective solutions to help the stakeholders of the railway transportation ecosystem overcome the challenges of providing safe and efficient transportation.
Integrating the most advanced measurement and telecommunication technologies, Candid offers its Railway Diagnostic product line, including the eRDM – Dynamic Railway Diagnostic System.
INCREASED SAFETY
Detection and alarm on derailment-hazardous (dangerous) dynamic load conditions of the passing trains.
OPERATING COST REDUCTION
Detection, trend-monitoring and alarm on railcar-, and infrastructuredamaging conditions of the passing train that results in:
- The preservation and lifetime extension of both the infrastructure and the rolling stocks by reduced and controlled wear and tear.
- Decreased maintenance costs by predictive maintenance based on the provided trend data.
BUSINESS EFFICIENCY AND PROFITABILITY
- Effective traffic management due to adaptive speed limitations, based on the detected dynamic load conditions.
- Increased utilization by predictive maintenance based on the provided trendmonitored data.
- Increased income by selling trend-monitored data for predictive maintenance purposes to other parties of interest.
- Quality-based tolls and payments based on the provided trend-monitored data.
- Real weight-based tolls and payments and real-time checking of the contracted weights with high accuracy and efficiency even at high train speeds.
ENVIRONMENTAL PROTECTION
Controlled noise-, and vibration-emission using defective wheel detection and trend-monitoring.
Functions
- TRAIN-, AND RAILCAR-WEIGHING
- at train speeds of up to 160 km/h
- within an accuracy of 2% (TÜV Certified)
- SPEED MEASUREMENT within an accuracy of 1%
- TEMPERATURE MEASUREMENT (optional)
- DAMAGE & DERAILMENT PREVENTION
- Detection, trend-monitoring & alarm of:
- Improper loading of axles, bogies- and railcars (overloading and all kinds of asymmetrical-loadings)
- Axle rupture
- Bogie suspension defect
- Wheel geometry defects (oval, eccentric, flat or polygonal wheels)
IN-MOTION WEIGHING
Using numerical analysis of the dynamic wheel loads measured by the eRDM system, the static weight of the railcars can be determined with high accuracy. Comparing the measured values with the available freight protocols, the eRDM system is able to verify the contracted freight in real time and send alert messages when overloading is detected. It also provides an alternative to weighbridges but way more cost effectively; even at high train speeds.
DETECTION AND DIAGNOSTICS
The eRDM system is able to detect and diagnose several defects of the passing train. Using trend-monitoring of the bogie-suspension or wheel-geometry conditions over time, it is possible to accomplish the maintenance of the rolling stocks on a predictive basis instead of conventional regular inspections. Predictive maintenance significantly reduces the idle time of the service, thus reduces operational costs and increases utilization.
Improper Wagon Loadings

Overloading
Overloading may cause derailment hazard, and might be damaging both for the infrastructure and the rolling stocks.
Asymmetric Load Conditions
Various asymmetrical load conditions of a railcar: left-right, front-rear, twisted wagons, symmetry within one bogie, etc.
Axle Rupture
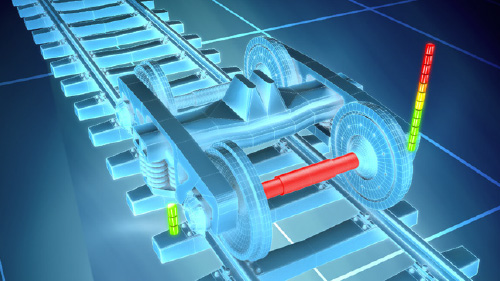
Running with ruptured axle is one of the most dangerous conditions for a train; therefore its detection has fundamental importance in regards to derailments. Axle rupture typically results in extreme asymmetrical load distribution between the wheels within the damaged axle.
Bogie Suspension Defect
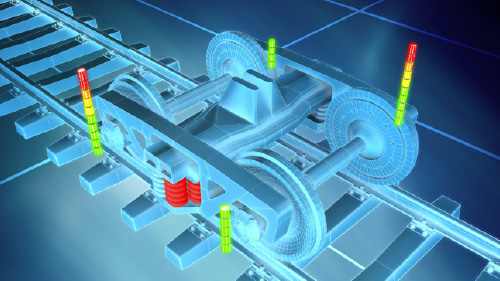
The fatigue of the suspension springs of the bogies also poses a derailment hazard as it typically results in an asymmetrical load distribution.
Defects in Wheel Geometry
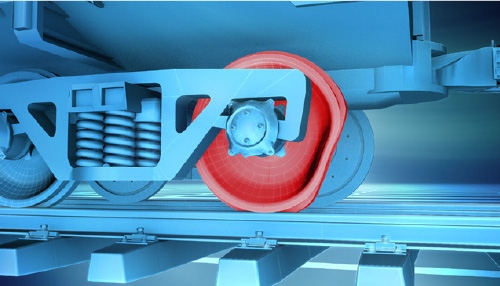
The geometrical deformation of the wheels causes periodic transient extra-loads, which might be damaging both for the infrastructure and for the rolling stock suspension and bearings. The eRDM system records the high resolution load response signal of each wheel and analyzes the wheel shape.
System description
eRDM is a highly integrated wayside digital sensor network system, with high resolution recording of the dynamic load response of each wheel of the passing train.
The dynamic load measurement is based on load measurement modules containing high accuracy, proprietary strain-gauge sensors integrated with high performance digital signal processors.
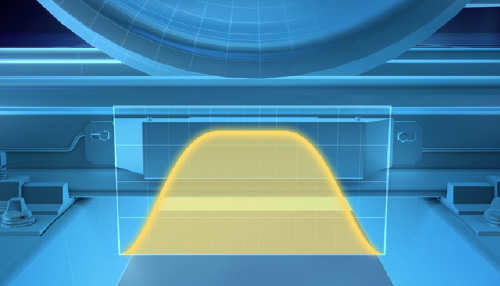
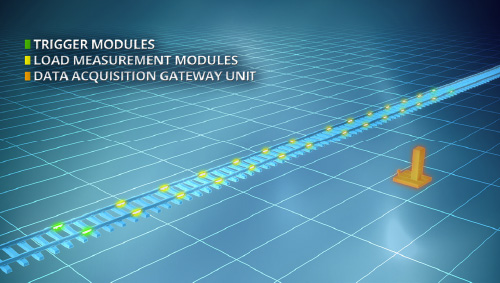
System architecture
The measurement section is composed of 12 pairs of load measurement modules and 2 pairs of train detection trigger modules to start the recording, all mounted on the web of the rail, and interconnected with a high-speed digital communication cable.
The measured high resolution load response signals are sent to the data acquisition and communication module located near the measurement section. The module has a battery equipped power supply and a wide area network connection (GSM, GPRS, HSPA, DSL etc.) The system analyses the measured axle-time profile using the offline vehicle database. The data acquisition module can be accessed by local Ethernet or Wi-Fi terminal by service maintenance personnel.
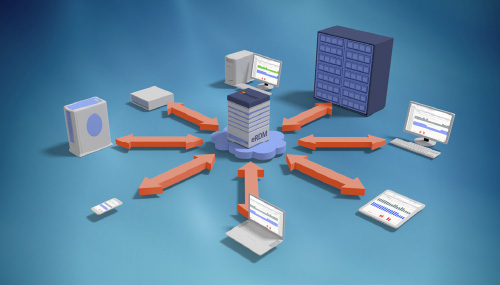
Several wayside eRDM systems can be integrated into a redundant high availability diagnostic server solution. The server collects, stores, processes, and analyzes the measurement results and sends the alarm and warning signals to client computers installed in operational stations. The central system can be accessed by various web browser applications.
Calibration & self-calibration
Calibration can be accomplished with wagons measured on high precision weighing systems. The service interface of the eRDM system manages the entire calibration process. The system performs regular self-checking and self-testing functions by comparing the measured and collected offline technical data of locomotives.
Services
Candid offers highly customized turnkey software development services for the integration of the eRDM system central diagnostic server into the IT system of the railway operator for integrated monitoring and alarm functionality.
Features
- Bi-directional measurement and detection
- Automatic and continuous self-calibration function
- Automatic and continuous self-diagnostics with remote maintenance function
- High reliability with a redundant system design (12 pairs of measurement modules)
- Noise immunity through integrated digital signal processor in each load measurement module
- High-resolution load response analysis with proprietary, high bandwidth digital communication
- End-to-end data security of measurement values with state-of-the art secure digital architecture
- Customized software integration into railway operator IT system
- Comprehensive diagnostics from single wheels to full train with automatic alarm functions
- Real-time train identification
- Low power consumption: - Can be powered from the signaling system; no need for overhead cable supply
- Battery powered UPS for enhanced availability
- Can be installed on most common existing rail systems cost-effectively, no need for special understructure
- Available also as Service on BOO basis
Parameters
- Axle load: 10 ÷ 400 kN (~ 1 ÷ 40 t)
- Weighing accuracy (on wagon basis): ±2 % (TÜV certified)
- Vehicle speed: 5 ÷ 160 km/h
- Speed measurement accuracy: 1%
- Electric supply: 230 (190-250) V; 50/75 Hz
- Electric power consumption: max. 150 VA (during measurement)
- Operational temperature range: -25°C…+60°C
- Length of measuring section: 34,2 m (with 600 mm railroadsleeper distance)
- Module environmental protection: IP67
- Minimal lifetime: 10 years
- MTBF: 10.000 hrs.
- Wheelbase: 700 mm min.
- Wheel diameter: 350 – 1250 mm
- Rail type (UIC): 48, 49, 54, 60
- Railroad sleeper distance: 580-650 mm
- Internal accumulator capacity: 12Ah